Plastic Injection
Theplastic injection is defined by the process of implementation of thermoformable materials, and more specifically thermoplastic materials. It makes it possible to obtain in one task, finite parts, complex shapes.
Uses the injection molding is a small, medium or very large series of parts manufacturing technique. These parts are then used for the automobile, the appliances, the furniture or even the computer equipment
Plastic injection Process
The plastic is melted and brought to a high temperature and then injected into a mould.
The Plastic injection mouldis usually made up of a fixed part stowed on the press, a movable part which will be articulated to allow the release of the part when it has cooled and an ejection system which has the Responsibility to propel the part out of the mould.
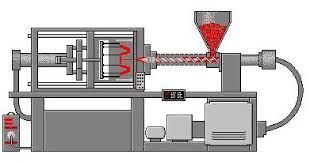
The injection Press checks the speed as well as the injection pressure of the material in the mould.
Unlike casting metal parts, it takes less than a minute to design a piece with injected plastic.
The impression of the mould is very fast filled for small parts and for larger parts, it is necessary to wait a few seconds.
Then we move on to the compaction phase during which the press puts the imprint under pressure by injecting more material to fill the removal of the plastic.
Finally, the parts from the plastic injection are expelled outside the mould by the ejection battery.
The Plastic injection mould
The moulds present on the plastic injection presses are composed of two shells which are called fixed part and movable part. These shells are strongly pressed against each other during the Molding, then discarded to allow ejection of the molded part. The mold may also have one or more cores used to form the hollow surfaces of the workpiece. There are also punches that make it possible to reserve openings in the walls of the room.
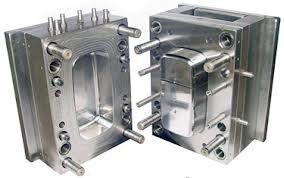
Injection Molding
Almost all thermoplastics can be molded by injection. It is possible to mould some thermosetting and metal powders into a thermoplastic matrix.
Although plastic injection molding produces very quickly small parts, the tooling is very expensive. The larger the molded parts, the longer they take time because the polymer cools down less quickly and must remain in the tool during cooling.